1> Pick up materials as planned. When picking up materials, carefully check whether the invoice is consistent with the physical code and quantity. The last part of materials B and A must be counted 100%. At least 10 trays of C materials must be taken. If errors are found during the issuance and retrieval process, they should be solved immediately on site. If the problem cannot be solved, report it to the direct supervisor and planning supervisor immediately for coordination and resolution. Do not delay and affect production.
2>Class A needs to pick up the materials that Class B will put online in advance and prepare them in advance.
3> All materials must be stamped by IQC, bulk materials must have IQC signature, the serial number and quantity cannot be erased on the bulk material label, and it must be confirmed that each tray of bulk materials can only have one section of material before it can be taken out.
4>Steel mesh and stickers must be brought into the material group together with the nesting materials. When the steel mesh is taken out, it should be confirmed whether it is damaged or otherwise abnormal. If there are any abnormalities, it should be confirmed on the spot and the engineering personnel should be contacted to confirm whether it can be used normally to avoid affecting production.
5>Pick materials to the material group and fill in the order tracking form.
6>When making accounts, the handwriting must be neat and complete, and there should be no clerical errors.
7> Timely update the missing materials and replenishing materials and prepare the “Material Shortage Report” and “Material Status List”, and report it to the plan to confirm the arrival time of the missing materials and inform the supervisor on duty.
8> After receiving the nesting materials, the production line material clerk will prepare the pre-production materials one day in advance according to the production plan. When preparing materials, carefully check the BOM and ECN to ensure that the material number, specification, and quantity of the materials to be put online are accurate.
9>B&C materials are distributed to the production line at one time. Precious components and PCB materials are distributed based on the actual production of the shift. Reel ICs can be distributed in the entire tray (minimum number of packages).
10>The PCB one-time distribution production line must not exceed the mouth of the blue plastic box.
11>The unpacked A material/PCB is sent to the production line first, and the humidity sensor must be tracked with a humidity sensor identification card.
12>When the printing station exchanges an empty bottle for new solder paste, it is required that the solder paste in the empty bottle is used up.
13> After issuing the set order to the production line for normal production for 4 hours, require/supervise the production line to pick up bulk materials (bags), and effectively control material loss.
14>Registration and control of the use of auxiliary materials and smelting tools. (Gloves, pen refills, tin wire, etc. must be replaced with new ones) Other customers require double-sided reuse before replacement.
15> When the solder paste is sent to the production line, the solder paste mixing record must be filled in and the recipient must be supervised to stir for 3-5 minutes before it is allowed to be used.
16>Monitor the daily handover of PCB and IC to ensure that differences are found on duty.
17> Solder paste is used according to the production plan. Try to share a bottle of solder paste between 2 or 3 lines of the same process. It should be used after use. The use time should not exceed 12 hours. Unless the production line is stopped, otherwise it is not allowed. Half a bottle of solder paste was withdrawn from the warehouse.
18> The material clerk for the over-order issued by the production line must confirm whether the over-order quantity meets the production requirement and confirm that it is OK before replenishing the material.
19> Before each shift ends, the IC materials must be inventoried and handed over to another shift.
20>The material clerk must check all the solder paste on the production line half an hour before leaving get off work, and no solder paste that has exceeded the use time is allowed to be left for another shift.
21> When the steel mesh needs to be returned to the material team after the production line is settled, the material clerk must confirm whether the steel mesh is damaged. If there is any damage, immediately notify the supervisor on duty and help find the relevant person responsible.
22> For warehouse over-delivered production line materials, the order materials must be returned to the warehouse within 12 hours after the production line is settled. For materials with too much excess damage, the reasons must be found and improvement measures must be found.
1> Before starting programming, the programmer must first check whether the device is well grounded.
2>The programmer must wear an anti-static ring. The anti-static ring should be close to the back of the hand. Gold and silver jewelry is not allowed.
3>The programmer should handle the IC with care to prevent the IC pins from being crooked or broken.
4> Burning OK/to-be-burned items must be placed strictly according to the marked area on the work surface, and the burning status, such as order number, software version, IPQC signature and other information, should be noted on the burned IC disk.
SMT key quality control position SOP
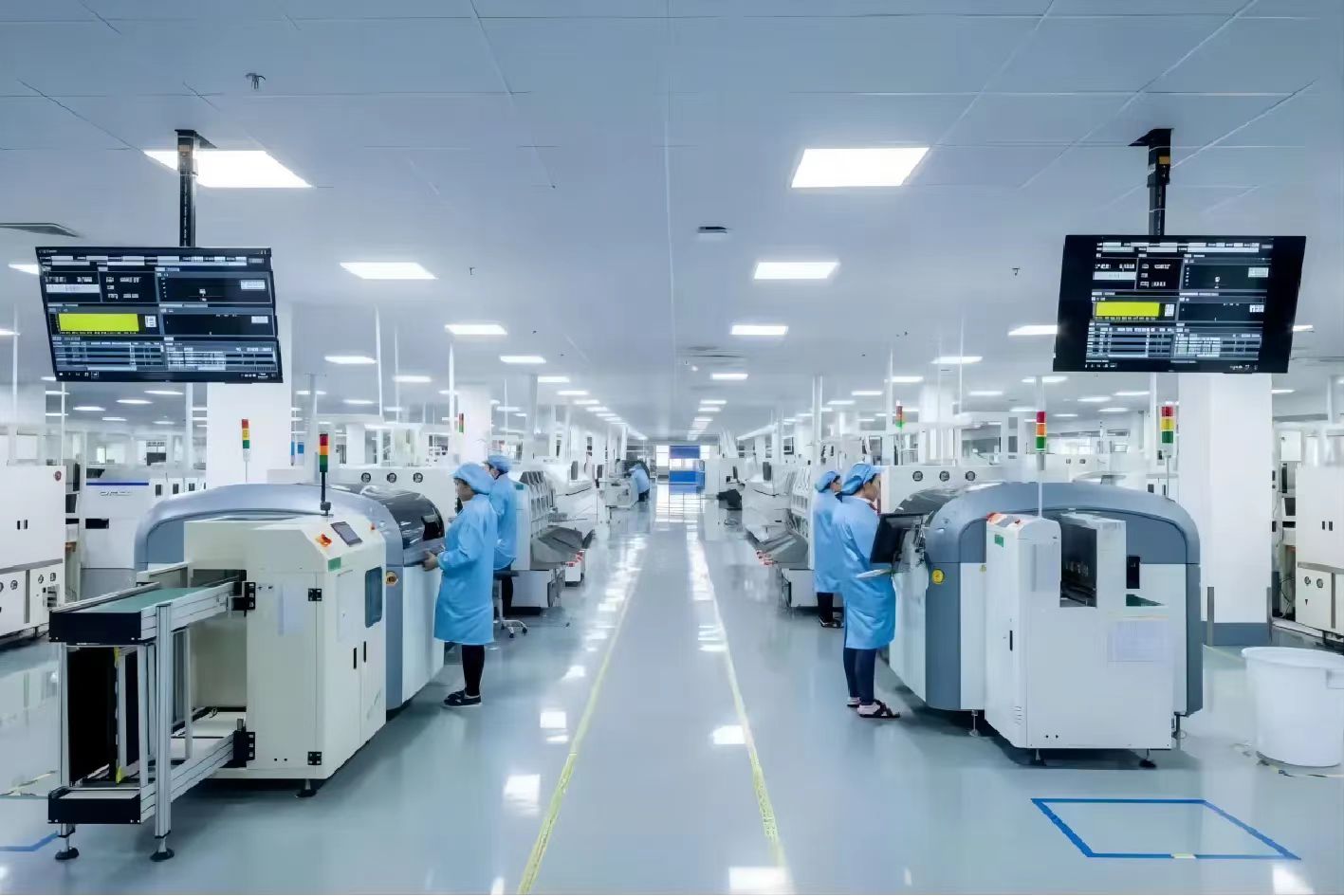
12
Dec